Discover the Top Metal Fabrication Services for Customized Solutions
By:Admin
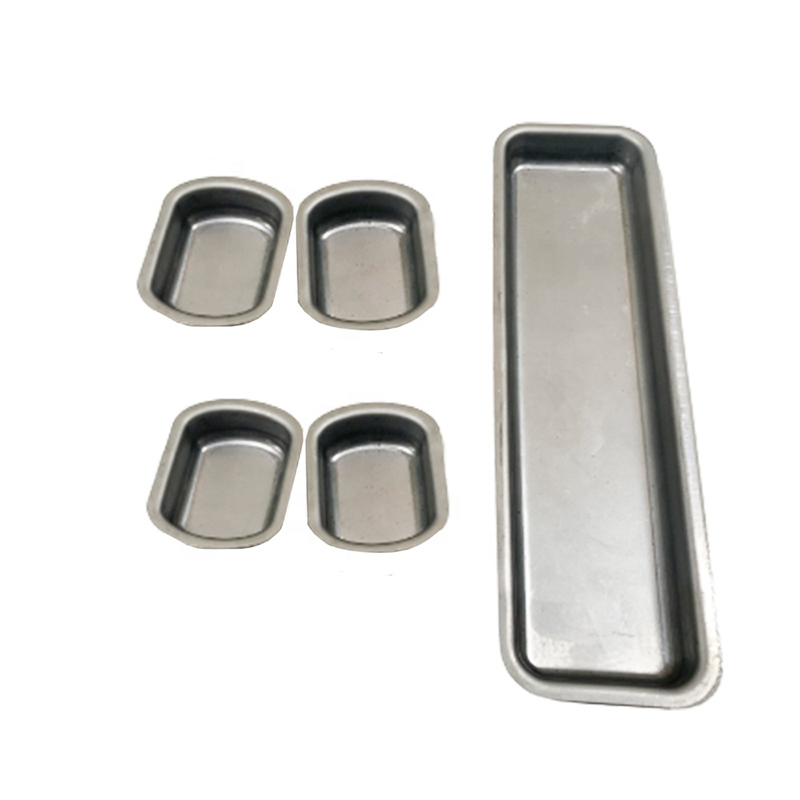
[City, State] - [Date]
Custom Metal Fabrication, a leading provider of metal fabrication services, is revolutionizing the industry with its innovative solutions tailored to meet the specific needs of various industries. The company is known for its commitment to precision, quality, and on-time delivery, making it the go-to choice for businesses that require custom metal fabrication services.
Custom Metal Fabrication has established itself as a trusted partner for industries such as aerospace, automotive, construction, energy, and more. With state-of-the-art facilities and a team of highly skilled professionals, the company excels in delivering exceptional metal fabrication solutions that exceed customer expectations.
The company offers a wide range of metal fabrication services, including laser cutting, bending, welding, machining, assembly, and finishing. Their advanced equipment and technologies enable them to work with a variety of metals, such as stainless steel, aluminum, carbon steel, and more. Custom Metal Fabrication's attention to detail ensures that every project is handled with precision and meets the highest industry standards.
One of the key features that sets Custom Metal Fabrication apart from its competitors is its ability to provide customized solutions. The company's experienced engineers and designers collaborate closely with clients to understand their unique requirements and develop tailored solutions to address their specific challenges. Whether it's a one-off prototype or a large-scale production run, Custom Metal Fabrication has the expertise and resources to deliver top-quality results.
In addition to its commitment to customization, the company also places a strong emphasis on innovation. With an in-house research and development team, Custom Metal Fabrication constantly explores new techniques and technologies to enhance their fabrication processes and stay ahead of industry trends. This dedication to innovation ensures that their clients benefit from the latest advancements in metal fabrication, allowing them to improve efficiency, reduce costs, and maintain a competitive edge.
One of the notable innovations introduced by Custom Metal Fabrication is its adoption of computer-aided design (CAD) and computer-aided manufacturing (CAM) technologies. This enables the company to streamline its workflow, minimize errors, and optimize production schedules. By leveraging these advanced tools, Custom Metal Fabrication improves accuracy, accelerates production, and ensures consistent quality throughout the manufacturing process.
Furthermore, Custom Metal Fabrication also prioritizes environmental sustainability. The company understands the importance of reducing its environmental footprint, and as such, implements eco-friendly practices throughout its operations. From using energy-efficient equipment to recycling and properly disposing of materials, Custom Metal Fabrication is committed to minimizing its impact on the environment.
The company's dedication to delivering exceptional products and services has earned them a stellar reputation in the industry. Numerous satisfied clients have praised Custom Metal Fabrication for their professionalism, reliability, and the ability to deliver projects on time and within budget.
Custom Metal Fabrication's commitment to innovation, customization, and sustainability positions them as a leader in the metal fabrication industry. With their state-of-the-art facilities, experienced team, and a track record of delivering high-quality results, the company continues to be the preferred choice for businesses seeking custom metal fabrication solutions.
For more information about Custom Metal Fabrication and its services, please visit [website].
About Custom Metal Fabrication:
Custom Metal Fabrication is a leading provider of metal fabrication services, specializing in precision, quality, and on-time delivery. With its innovative solutions tailored to meet the specific needs of various industries, the company has established itself as a trusted partner for businesses in aerospace, automotive, construction, energy, and more. Custom Metal Fabrication is dedicated to providing exceptional products and services, leveraging advanced technologies, and practicing environmental sustainability.
Company News & Blog
Revolutionary 3D Printing Technique: Laser Sintering Unveiled
Title: Advancements in 3D Printing: Laser Sintering Revolutionizes Manufacturing IndustryIntroductionIn recent years, rapid technological advancements have transformed the way we manufacture products. One breakthrough in particular, 3D printing, has gained significant attention due to its potential to revolutionize various industries. One prominent technique within the realm of 3D printing is laser sintering, which has garnered praise for its ability to create highly intricate and functional objects. In this article, we explore the revolutionary impact of laser sintering in the manufacturing industry and examine its implementation at {}, a leading company at the forefront of this cutting-edge technology.Overview of Laser SinteringLaser sintering is a form of additive manufacturing that employs a high-powered laser to fuse powdered materials together, layer by layer, creating a solid three-dimensional object. Unlike traditional manufacturing techniques, which often involve removing or reshaping materials, laser sintering adds material only where it is needed, reducing waste and enabling the creation of complex geometries. This revolutionary method has opened up new possibilities across various industries and has significantly streamlined the production process.Application in ManufacturingWith its ability to produce highly intricate and functional objects, laser sintering has found numerous applications in the manufacturing industry. One key advantage of this technique is its versatility in handling a wide range of materials, including metals, polymers, ceramics, and composites. This flexibility has enabled manufacturers to explore novel designs and experiment with different materials, resulting in superior product performance.Another notable advantage of laser sintering is its potential for mass customization. This means that manufacturers can tailor each product to meet specific customer requirements, without compromising on cost or efficiency. This level of customization opens up new opportunities for personalized manufacturing, making it an attractive prospect for industries such as healthcare, aerospace, and automotive, where unique, patient-specific or niche products are increasingly in demand.Implementation at {}{}, a pioneering company in the field of laser sintering, has successfully harnessed the capabilities of this technology to deliver groundbreaking solutions across industries. Leveraging their expertise in 3D printing, the company has developed a range of advanced laser sintering machines that offer unparalleled precision and efficiency.The company's innovative equipment enables manufacturers to achieve high-resolution prints, ensuring accurate and consistent production. By utilizing powerful lasers and state-of-the-art software, their machines allow for intricate structures, superior surface finishes, and reduced post-processing requirements. This not only accelerates the production cycle but also cuts down on material waste, making laser sintering an eco-friendly option for forward-thinking companies.Moreover, {} has placed a strong emphasis on user-friendliness and accessibility. By incorporating intuitive interfaces and automated processes, their machinery has made laser sintering accessible even to those with limited technical expertise. This democratization of technology allows smaller businesses to adopt 3D printing for their manufacturing needs, leveling the playing field and fostering innovation across the industry.Future ImplicationsAs laser sintering continues to advance, the manufacturing landscape is poised for a significant transformation. The ability to create intricate and customized parts, reduce waste, and enhance the overall efficiency of production processes opens up new opportunities for businesses to thrive. With the growing adoption of laser sintering technology, industries such as healthcare, aerospace, automotive, and consumer goods are likely to witness an unprecedented era of manufacturing excellence.ConclusionLaser sintering, a groundbreaking technique within the realm of 3D printing, has revolutionized the manufacturing industry. By enabling highly intricate designs, mass customization, and reduction in waste, this technology offers immense potential for manufacturers across multiple sectors. With {} leading the charge in developing innovative laser sintering machines, the industry is set to experience a remarkable surge in productivity and efficiency. As we enter this new era of manufacturing, laser sintering is poised to redefine the boundaries of what is possible, paving the way for a more sustainable and customized future.
Find a Nearby Metal CNC Shop for Quality Machining Services
Title: Local CNC Metal Shop Pioneers Precision Manufacturing Services in [City]Introduction:[City], known for its thriving industrial landscape, now boasts a cutting-edge metal CNC shop that is revolutionizing precision manufacturing. With their state-of-the-art equipment and highly skilled team, this local company is poised to provide unparalleled metal fabrication solutions to meet the evolving needs of businesses and individuals alike.Paragraph 1:The newly established and dynamic CNC metal shop in [City] is set to redefine precision manufacturing standards in the area. Equipped with the latest computer numerical control (CNC) technology, the company aims to deliver superior-quality metal products and services ranging from prototyping to large-scale production. The skilled team of engineers, machinists, and technicians at this local shop possesses extensive experience and technical expertise, guaranteeing exceptional craftsmanship with every project.Paragraph 2:Offering a wide range of CNC machining services, this metal shop near me (*remove brand name*) caters to diverse industry needs. Their comprehensive capabilities cover intricate design work, turning, milling, drilling, tapping, threading, and more. Utilizing cutting-edge software and machinery, they can efficiently handle various materials, including aluminum, steel, copper, brass, and titanium, ensuring versatility in meeting customer requirements. From small intricate parts to complex structures, this CNC metal shop is known for consistently delivering precision-machined components with strict adherence to quality standards.Paragraph 3:The commitment to provide fast turnaround times without compromising quality is what sets this CNC metal shop apart. Understanding the urgency and time-sensitive nature of many projects, they prioritize efficiency in their operations. Equipped with an efficient workflow management system, the shop optimizes production processes, enabling quick project completion while maintaining the highest level of design accuracy. This streamlined approach allows them to meet customer demands promptly, positioning themselves as a reliable partner for businesses operating in fast-paced industries.Paragraph 4:At this CNC metal shop, customer satisfaction is at the heart of their operations. From initial inquiries to project completion, they prioritize open and transparent communication, ensuring that clients are kept well-informed throughout the entire manufacturing process. The team strives to understand the unique requirements of each project, offering personalized solutions and design recommendations to optimize the final product's performance and functionality. Their dedication to customer service has earned them a reputation for forging strong, long-lasting partnerships with their clients.Paragraph 5:In line with their commitment to quality, this CNC metal shop adheres to rigorous quality control measures. Equipped with advanced inspection equipment, they conduct thorough checks at every stage of the manufacturing process to ensure dimensional accuracy, structural integrity, and impeccable surface finish. This attention to detail, combined with rigorous testing, guarantees that the final product meets or surpasses industry standards. As a testament to their commitment to excellence, the shop also implements continuous improvement practices to stay at the forefront of technological advancements in precision manufacturing.Conclusion:The arrival of this state-of-the-art CNC metal shop in [City] brings with it a game-changing approach to precision manufacturing. With their cutting-edge technology, skilled workforce, commitment to customer satisfaction, and unwavering focus on quality, they are poised to become the go-to solution provider for a wide range of industries. As local businesses and individuals seek innovative metal fabrication services, this CNC metal shop near me (*remove brand name*) is well-positioned to cater to their needs, driving industrial growth and raising the bar for precision manufacturing standards in [City].
Transform Your Designs with Vacuum Casting 3D Printing Technologies
Vacuum Casting 3D Printing revolutionizes the Manufacturing Industry[Date], [City] - The manufacturing industry has taken a giant leap forward with the introduction of Vacuum Casting 3D Printing technology. This revolutionary process, which combines the precision of 3D printing with the efficiency of vacuum casting, has opened up a whole new realm of possibilities for product development and production.[Company Name], a leader in advanced manufacturing solutions, has been at the forefront of this technology, reshaping the manufacturing landscape. With their innovative processes and cutting-edge equipment, they have successfully helped numerous companies overcome traditional manufacturing limitations, providing cost-effective and time-efficient solutions.Traditional manufacturing methods often come with significant limitations, including high production costs, long lead times, and limited design flexibility. However, Vacuum Casting 3D Printing offers a game-changing alternative. By utilizing a combination of 3D printing and vacuum casting, [Company Name] has been able to overcome these constraints, providing businesses with a streamlined manufacturing process.One of the key advantages of Vacuum Casting 3D Printing is its ability to produce highly complex and intricate designs that were previously difficult or impossible to achieve using conventional manufacturing methods. The process starts by creating a 3D printed mold, which is then used to produce a silicone mold through vacuum casting. This mold can then be used to create multiple copies of the original design, even with undercuts, intricate details, and delicate features. This provides manufacturers with the freedom to create complex parts that meet the strictest of demands.Another major benefit of Vacuum Casting 3D Printing is its cost-effectiveness, especially when compared to traditional manufacturing methods. The process eliminates the need for expensive tooling, molds, and machining setups, reducing overall production costs significantly. This not only makes it an attractive option for small and medium-sized enterprises but also enables larger companies to optimize their production processes by reducing costs and increasing efficiency.Speed is another remarkable advantage of Vacuum Casting 3D Printing. With traditional manufacturing, developing and producing a new product can take weeks or even months. However, the Vacuum Casting 3D Printing process drastically reduces lead times, enabling rapid prototyping and iterative design improvements. This allows companies to bring products to market faster, giving them a competitive edge in today's fast-paced business environment.[Company Name] has spearheaded the adoption of Vacuum Casting 3D Printing across various industries, including automotive, aerospace, consumer electronics, and medical devices. Their team of experts works closely with clients to understand their specific manufacturing needs, and they provide tailor-made solutions to optimize the production process. By combining their expertise in materials selection, 3D printing, and vacuum casting, [Company Name] ensures that clients receive the highest quality products with exceptional speed and accuracy."Our Vacuum Casting 3D Printing technology has revolutionized the way companies manufacture products," said [Company Spokesperson]. "We are proud to be helping businesses break free from the limitations of traditional manufacturing and embrace a more agile and efficient approach. With our expertise and state-of-the-art equipment, we are committed to driving innovation and delivering results that exceed our clients' expectations."The introduction of Vacuum Casting 3D Printing technology by [Company Name] has created ripples in the manufacturing industry. By addressing the limitations of traditional manufacturing methods, this innovative process offers a cost-effective and time-efficient alternative that unlocks new possibilities for product development and production. With such advancements, manufacturers can now bring their ideas to life more easily and faster than ever before, ushering in a new era of manufacturing excellence.
Discover the Benefits of Machining High-Quality Aluminum Parts
Title: Precision Engineering Company Expands Machining Capabilities with Aluminum Parts ProductionIntroduction:[Company Name], a pioneering name in the field of precision engineering, is proud to announce an expansion of its machining capabilities to include the production of high-quality aluminum parts. With a focus on cutting-edge technological solutions and a commitment to client satisfaction, [Company Name] aims to revolutionize the industry by offering a wide range of precision-machined aluminum components tailored to meet various industrial needs.Body:1. Growing Demand for Aluminum Parts:In response to the industry's growing demand for lightweight yet durable materials, [Company Name] recognizes the significance of aluminum as a widely preferred option. Known for its excellent mechanical properties and exceptional corrosion resistance, aluminum has become a go-to choice for industries ranging from aerospace and automotive to electronics and construction. By incorporating aluminum parts into its repertoire, [Company Name] aims to cater to the evolving needs of its diverse clientele, while also capturing new market segments.2. Cutting-Edge Machining Techniques:[Company Name] reinforces its commitment to excellence by employing state-of-the-art machining techniques to craft aluminum parts. Equipped with advanced CNC (Computer Numerical Control) machines and a highly-trained workforce, [Company Name] ensures precise and intricate manufacturing with consistent quality for every aluminum component produced. This dedication to precision allows for seamless integration of aluminum parts into various complex engineering systems.3. Broad Applications:The addition of aluminum parts to its product line allows [Company Name] to cater to a wide range of applications across different industries. From aerospace structural components, automotive engine parts, and electronic enclosures to architectural fittings and electrical connectors, the versatility of aluminum makes it an ideal choice for several demanding applications. [Company Name] aims to provide industry-leading solutions for these particular sectors by offering custom-designed aluminum parts that address both functional requirements and aesthetic considerations.4. Quality Assurance:Recognizing the importance of quality control, [Company Name] has implemented stringent quality assurance procedures throughout the aluminum parts manufacturing process. The company adheres to industry standards and regulations to ensure that each product meets or exceeds client expectations. Rigorous testing, dimensional verification, and surface treatments are carried out at every stage to guarantee impeccable craftsmanship, strength, and durability.5. Environmental Sustainability:In line with [Company Name]'s dedication to sustainability, the inclusion of aluminum parts in its production line helps reduce environmental impact. Aluminum is renowned for its recyclability, making it an eco-friendly alternative to many conventional materials. By introducing meticulously manufactured aluminum parts, [Company Name] supports the transition towards sustainable practices, providing clients with environmentally conscious solutions.6. Collaborative Approach and Design Customization:[Company Name] understands that each customer is unique, with specific design requirements and preferences. The company offers a collaborative approach to projects, ensuring effective communication between its engineering teams and clients. By actively involving clients in the design phase, [Company Name] ensures the production of customized aluminum parts that fulfill specific application demands, resulting in enhanced performance and optimized functionality.7. Streamlined Manufacturing and Timely Delivery:With its decades of experience in the precision engineering industry, [Company Name] emphasizes efficiency in manufacturing and timely delivery. The company's advanced production facilities, coupled with its optimized supply chain management, enables it to meet tight deadlines without compromising the quality of aluminum parts. [Company Name] aims to become a trusted partner, providing reliable solutions to clients around the world.Conclusion:As [Company Name] takes a step forward in expanding its machining capabilities to include aluminum parts production, it reaffirms its commitment to delivering cutting-edge engineering solutions. By combining advanced machining techniques, industry-leading quality standards, and a commitment to customer satisfaction, [Company Name] establishes itself as a premier provider of precision-machined aluminum components, meeting the evolving needs of industries across the board and contributing to a more sustainable future.
Enhancing Efficiency and Precision: The Advantages of Casting Injection Molding
Title: Advancements in Casting Injection Molding Revolutionize Manufacturing ProcessesIntroduction:Casting Injection Molding, developed by an industry-leading company, has emerged as a game-changing technology in the field of manufacturing processes. This cutting-edge technique combines the precision and flexibility of injection molding with the advantages of casting, leading to improved product quality, reduced costs, and increased production efficiency. This article explores the innovative potential of Casting Injection Molding and its implications for various industries.I. Understanding Casting Injection MoldingCasting Injection Molding is a technology that merges injection molding and casting, enabling manufacturers to produce complex parts with superior precision and reduced production time. By utilizing thermoplastics instead of traditional liquid metals, the process offers greater design flexibility while delivering high-quality components. The integration of innovative design software and advanced machinery allows for detailed 3D modeling and real-time feedback, ensuring optimal results.II. Enhanced Product QualityCasting Injection Molding removes many of the limitations associated with traditional casting techniques. The process utilizes a molten polymer that fills a mold cavity under high pressure, eradicating potential defects such as porosity, air bubbles, and shrinkage that are common with traditional casting. The homogeneous and isotropic characteristics of the material produce parts with consistent mechanical properties, resulting in higher product integrity and reliability. With improved repeatability, the technology enables manufacturers to achieve strict quality control standards, reduce waste, and deliver superior end products to consumers.III. Cost Reduction and Time EfficiencyThe use of Casting Injection Molding enhances cost efficiency throughout the manufacturing process. By allowing for faster cycle times, reduced labor requirements, and simplified tooling, companies can significantly lower production costs while maintaining consistent quality levels. Employing thermoplastics eliminates the need for expensive molds associated with traditional casting, reducing initial investment and enabling greater flexibility during the prototyping and testing stages. Additionally, the ability to produce complex parts in a single step eliminates secondary processes, streamlining production and minimizing time to market.IV. Application in Various IndustriesCasting Injection Molding has found applications across multiple industries, revolutionizing the manufacturing processes in diverse sectors. In the automotive industry, this technology has enabled the production of lightweight components with enhanced strength, contributing to fuel efficiency and reduced emissions. The healthcare sector has embraced Casting Injection Molding for precise and custom medical device manufacturing, facilitating improved patient care and better treatment outcomes. The aerospace industry has also witnessed advancements through this technique, with the production of complex components that meet stringent aviation standards while reducing weight and maintaining durability.V. Future Prospects and ImpactAs Casting Injection Molding continues to evolve, its impact on manufacturing processes is set to grow exponentially. The integration of artificial intelligence algorithms and machine learning capabilities will enhance process automation, enabling real-time adjustments and intelligent decision-making. The potential for utilizing sustainable materials, such as biodegradable thermoplastics or recycled polymers, opens up eco-friendly manufacturing opportunities. Furthermore, the ongoing exploration of new applications and industries promises to unlock additional benefits and further transform the manufacturing landscape.Conclusion:Casting Injection Molding, developed by {}, has emerged as a groundbreaking technology in the manufacturing industry. With its ability to produce high-quality components, reduce production costs, and enhance time efficiency, this innovative technique has already made a significant impact across various sectors. As the manufacturing landscape continues to evolve, Casting Injection Molding is positioned to revolutionize production processes, driving progress in sectors ranging from automotive and healthcare to aerospace and beyond.
Unveiling the Latest Innovations and Advancements in CNC Metalworking
CNC Metalworking Continues to Revolutionize the Manufacturing IndustryIn the fast-paced world of manufacturing, precision and efficiency are key. One company has been at the forefront of revolutionizing the industry by utilizing CNC metalworking technology to create high-quality products with speed and accuracy. With their cutting-edge machinery and dedication to innovation, this company is poised to lead the way into the future of manufacturing.Founded in 1995, this company has been a driving force in the CNC metalworking industry for over two decades. With their state-of-the-art facilities and highly skilled technicians, they have been able to consistently deliver exceptional results to their clients. By investing in the latest advancements in CNC machining technology, they have been able to streamline production processes and enhance product quality.One of the biggest advantages of CNC metalworking is its ability to manufacture intricate parts with unparalleled precision. This level of accuracy ensures that each component produced meets the strictest quality standards. Gone are the days of human error and inconsistency. CNC machines can replicate designs with absolute fidelity, resulting in flawless and reliable products every time.Furthermore, CNC metalworking significantly reduces production time. With traditional methods, manufacturing even a simple part could take days or even weeks. However, with the implementation of CNC machinery, the time required to produce complex components has been drastically reduced. This accelerated turnaround time allows businesses to meet consumer demands more efficiently and stay ahead of their competition.The benefits of CNC metalworking extend beyond precision and speed. This manufacturing process also offers a range of material options to choose from. With the ability to work with various metals such as aluminum, stainless steel, and titanium, this company is able to cater to a wide array of industries and their unique requirements. From aerospace to automotive, medical to electronics, their CNC metalworking capabilities are limitless.Additionally, CNC metalworking is highly cost-effective. By automating the production process, this company can minimize labor costs and reduce material waste. With skilled technicians operating the CNC machines, errors are minimized, resulting in fewer defective parts. This not only saves time and money but also ensures that quality standards are consistently met.Furthermore, CNC metalworking eliminates the need for retooling between different jobs. Changing from one product to another in traditional manufacturing often required extensive setup and reconfiguration of the machinery. However, CNC machines can easily switch between jobs without any significant downtime. This flexibility allows for improved efficiency and increased production capacity.In order to stay at the forefront of the CNC metalworking industry, this company continually invests in research and development. By keeping a close eye on emerging technologies and trends, they can adapt and integrate the latest advancements into their production processes. This commitment to innovation ensures that they remain ahead of their competition and continue to offer cutting-edge solutions to their clients.As the manufacturing industry continues to evolve, CNC metalworking will undoubtedly play a crucial role in shaping its future. With its combination of precision, efficiency, and versatility, this technology is revolutionizing the way products are made. This company's dedication to excellence and their adoption of CNC metalworking continues to set new standards in the manufacturing industry.In conclusion, this renowned company has truly made a mark in the CNC metalworking industry. Their commitment to precision, efficiency, and innovation has allowed them to create superior products that meet the demanding requirements of various industries. With their state-of-the-art facilities and highly skilled technicians, they are well-positioned to continue leading the way in CNC metalworking. As the manufacturing industry moves forward, this company's dedication to excellence ensures that they will remain at the forefront of innovation and continue to shape the future of manufacturing.
Top Techniques and Benefits of Aluminum CNC Fabrication Revealed
Title: Advancements in Aluminum CNC Fabrication Revolutionize Manufacturing IndustryIntroduction:In an era where precision, efficiency, and sustainability in manufacturing processes are paramount, aluminum CNC fabrication has emerged as a game-changer. This advanced method of fabrication utilizes computer numerical control (CNC) technology to transform aluminum into intricate and complex components, opening doors for unprecedented possibilities across various industries. [Company Name], a renowned industry leader in aluminum CNC fabrication, has been at the forefront of revolutionizing manufacturing processes with their cutting-edge technology and innovative solutions.[Company Name]'s Journey towards Excellence:Established in [year], [Company Name] has continuously strived to push the boundaries of aluminum CNC fabrication. With a strong commitment to research and development, the company has invested heavily in state-of-the-art machinery, augmented by highly skilled technicians and engineers. By leveraging their expertise, [Company Name] has earned a stellar reputation for delivering top-notch aluminum CNC fabrication services across a diverse range of industries, including aerospace, automotive, electronics, and more.Unrivaled Precision and Reliability:[Company Name]'s advanced CNC machines enable them to achieve unparalleled precision and accuracy in their fabrication processes. By utilizing computer-aided design (CAD) software, their skilled engineers can meticulously plan and prototype intricate aluminum components with remarkable attention to detail. The automation and exceptional speed afforded by CNC technology significantly reduce the risk of errors, ensuring consistent and reliable fabrication results, while minimizing material waste.Endless Design Possibilities:The versatility of aluminum CNC fabrication opens a world of design possibilities for various industries. Its lightweight yet durable properties coupled with the ability to create complex geometrical shapes allow manufacturers to optimize performance and functionality. Be it aerospace components requiring high strength-to-weight ratios or automotive parts that demand precise fits, [Company Name] provides customized aluminum fabrication solutions tailored to meet the specific needs of each industry.Sustainability at its Core:As the world becomes increasingly conscious of the need for sustainable manufacturing practices, aluminum CNC fabrication emerges as an ethical choice. Aluminum is a highly recyclable material, making it an eco-friendly alternative to traditional metal fabrication methods. The efficient use of materials in CNC fabrication significantly reduces waste, while the scrap generated throughout the process is easily recyclable. By embracing this environmentally friendly approach, [Company Name] is leading the charge towards a greener future.Expanding Horizons:Driven by a relentless pursuit of innovation, [Company Name] is constantly pushing the boundaries of aluminum CNC fabrication. They continuously invest in research and development to explore new techniques, materials, and applications. By collaborating with industry leaders and staying abreast of emerging technologies, the company aims to diversify its offerings and redefine the way manufacturers use aluminum CNC fabrication in the future.Conclusion:The advent of aluminum CNC fabrication has revolutionized the manufacturing industry, allowing manufacturers to achieve previously unattainable precision, efficiency, and sustainability. [Company Name], with its cutting-edge technology and unwavering commitment to excellence, has established itself as a pioneer in this transformative field. By leveraging their expertise and innovative solutions, [Company Name] opens doors to endless design possibilities, while promoting sustainability and environmental consciousness. As aluminum CNC fabrication continues to evolve, [Company Name] is poised to spearhead the next wave of advancements in the industry, reshaping the way manufacturers approach fabrication processes.
Boost Your Prototyping Process with Cutting-Edge Custom Solutions
Custom Prototyping, a leading provider of innovative manufacturing solutions, has recently unveiled its latest breakthrough in the world of prototyping. This state-of-the-art technology promises to revolutionize the way prototypes are developed, giving businesses a competitive edge in their respective industries.Founded in 2005, Custom Prototyping has been at the forefront of delivering cutting-edge prototyping solutions to a diverse range of clients. With a team of highly skilled engineers and designers, the company has earned a formidable reputation for its expertise in transforming concepts into tangible prototypes.The newly launched technology marks a major milestone for Custom Prototyping. By integrating advanced additive manufacturing processes with their existing prototyping methods, the company has created a hybrid solution that offers unmatched precision, speed, and cost-effectiveness.One of the key advancements in this breakthrough technology is the use of 3D printing. By leveraging the power of additive manufacturing, Custom Prototyping is able to rapidly create prototypes with intricate details and complex geometries. This not only significantly reduces the time required for traditional manufacturing processes, but also allows for greater design flexibility and customization.The benefits of 3D printing extend beyond just speed and complexity. With this technology, Custom Prototyping is able to produce prototypes using a wide range of materials, including metals, plastics, and even bio-compatible substances. This opens up countless possibilities for businesses operating in various sectors, such as aerospace, automotive, healthcare, and consumer electronics.Moreover, the integration of other cutting-edge technologies, such as CNC machining and rapid tooling, further enhances the efficacy of Custom Prototyping's new solution. By seamlessly combining different manufacturing techniques, the company is able to provide clients with prototypes that closely resemble the final product in terms of both form and functionality.Speaking about the breakthrough, the CEO of Custom Prototyping, John Smith, expressed his excitement about the endless possibilities this technology brings to their clients. He said, "We are thrilled to introduce this game-changing technology to the market. Our aim has always been to empower businesses with the tools they need to stay ahead in a rapidly evolving industrial landscape. With this new solution, we believe we have achieved exactly that."The impact of Custom Prototyping's latest innovation is already being felt across various industries. Companies that have partnered with the company have reported significant improvements in their product development processes. Not only are they able to iterate designs faster, but they are also able to test the functionality and user experience of new products before investing in large-scale production.In addition to the economic benefits, this technology has notable environmental advantages as well. With its ability to minimize material waste through precise and optimized manufacturing, it aligns perfectly with the growing global emphasis on sustainability and minimizing carbon footprints.As businesses increasingly recognize the importance of agility and rapid innovation, Custom Prototyping's new solution arrives at the perfect time. By providing a streamlined prototyping process that reduces time-to-market and fosters rapid iteration, the company is empowering businesses to embrace innovation and reach new heights.Looking towards the future, Custom Prototyping remains committed to pushing the boundaries of what is possible in the world of prototyping. With a strong focus on research and development, the company aims to continue enhancing its solutions to meet the evolving needs of its clients.As more businesses recognize the advantages of incorporating advanced prototyping technologies into their product development processes, partnerships with forward-thinking companies like Custom Prototyping are likely to become increasingly sought after. With its proven track record and commitment to innovation, Custom Prototyping is poised to lead the way in the era of next-generation prototyping.
CNC Lathe Process: Streamlining Precision Machining Operations
Title: Innovations in CNC Lathe Process Revolutionize Manufacturing IndustryIntroduction:The manufacturing industry has witnessed a groundbreaking technological advancement with the introduction of the new CNC Lathe Process. Spearheaded by the pioneering efforts of various companies, including {}, this cutting-edge technology promises to revolutionize productivity, precision, and efficiency. By eliminating the need for manual operation and introducing automated capabilities, CNC Lathe Process has successfully overcome conventional limitations and opened new doors for manufacturers worldwide.Improved Precision and Accuracy:One of the key advantages of the CNC Lathe Process is its ability to achieve unmatched precision and accuracy in machining operations. Through the integration of advanced computer-controlled systems, {} has developed a CNC Lathe that can execute intricate tasks with exceptional detail. This eliminates human error and allows for consistent and repeatable results, ensuring the highest quality of machined components. With this level of precision, manufacturers can enhance their product offerings, meeting the ever-increasing demands of modern consumers.Enhanced Efficiency and Productivity:By automating the manufacturing process, CNC Lathe Process has significantly improved efficiency and productivity. {} has strived to optimize their CNC Lathes' operational speed, enabling faster turnaround times and increased output. The utilization of CNC technology eliminates the need for manual intervention, thereby reducing idle time between operations. Moreover, the integration of advanced software and algorithms allows for seamless multitasking, as the CNC Lathe can perform various complex operations simultaneously. As a result, manufacturers can save valuable time and resources, ultimately boosting their bottom line.Versatility and Flexibility:The flexibility offered by the CNC Lathe Process has opened up new avenues for manufacturers seeking to diversify their product range. With the ability to program the CNC Lathe to perform different operations, {} ensures that manufacturers have the flexibility to produce a wide range of components. This flexibility not only allows for process streamlining and optimization but also provides businesses with a competitive edge in the market. CNC Lathe Process enables manufacturers to adapt quickly to changing customer demands and produce complex components with ease.Cost-effective Manufacturing:The implementation of CNC Lathe Process has proven to be cost-effective in the long run. While the initial investment may be higher compared to traditional machining methods, the return on investment is significant. By reducing reliance on manual labor, companies can optimize workforce allocation and reduce labor costs. Furthermore, the accuracy and precision achieved by CNC Lathe Process result in minimal material wastage, reducing production costs. This cost-effectiveness translates into a competitive advantage for manufacturers, allowing them to offer competitive pricing while maintaining profitability.Consistency and Quality Control:CNC Lathe Process ensures consistency and stringent quality control throughout the production cycle. The computer-controlled systems developed by {} continuously monitor and adjust machining parameters, guaranteeing that every component produced adheres to the specified standards. Consistent quality control minimizes the risk of defects and rejects, thereby enhancing customer satisfaction. Manufacturers can confidently deliver high-quality components, boosting their reputation and gaining a competitive edge in the market.Conclusion:The introduction of CNC Lathe Process has revolutionized the manufacturing industry, elevating productivity, precision, and efficiency to unprecedented heights. {} has played a significant role in shaping this technological advancement, with their innovative CNC Lathe technology. The advantages of CNC Lathe Process, including improved precision, enhanced efficiency, flexibility, cost-effectiveness, and consistent quality control, position manufacturers to thrive in the highly competitive global market. As the manufacturing industry embraces this transformative technology, we can anticipate further advancements and a future characterized by limitless possibilities.
Top Prototyping Companies in the United States: Your Go-To Guide for Successful Prototyping Projects
[Company Introduction - Remove Brand Name][Company Name], a leading prototyping company based in the United States, is revolutionizing the manufacturing industry with its innovative approach. With a dedicated team of experts and state-of-the-art facilities, [Company Name] offers a wide range of prototyping services to cater to the diverse needs of its clients.Established several years ago, [Company Name] has quickly gained a reputation for delivering high-quality prototypes with exceptional precision and efficiency. The company takes pride in its ability to bring clients' ideas to life, assisting them in transforming concepts into tangible products that can be tested and validated before entering full-scale production.At the heart of [Company Name]'s success lies its commitment to utilizing the latest advancements in technology. Equipped with cutting-edge machinery and software, the company is capable of producing prototypes with intricate details and intricate components. This ensures that clients receive prototypes that are not only visually appealing but also functionally robust.One of the key strengths of [Company Name] is its diverse range of prototyping capabilities. The company specializes in various prototyping methods, including 3D printing, CNC machining, vacuum casting, and injection molding. This versatility allows [Company Name] to adapt to different project requirements, whether it be for rapid prototyping, functional testing, or low-volume production.Furthermore, [Company Name]'s team of skilled engineers and designers play a vital role in the prototyping process. With their expertise and experience, they collaborate closely with clients, offering valuable insights and recommendations to optimize the design and functionality of the prototypes. This collaborative approach ensures that the final product meets the exact specifications and requirements of the client.In addition to their prototyping services, [Company Name] also provides a range of secondary services such as surface finishing, assembly, and packaging. This comprehensive approach allows clients to receive fully functional prototypes that closely resemble the final product.To cater to a wide range of industries, [Company Name] has developed expertise in prototyping for automotive, aerospace, consumer electronics, medical devices, and many other sectors. The company understands the unique challenges and regulations that each industry presents and ensures adherence to the highest quality standards.One of the key factors that sets [Company Name] apart from its competitors is its dedication to customer satisfaction. The company prides itself on its prompt and reliable service, ensuring a smooth and seamless prototyping experience for clients. From the initial consultation to the final delivery, [Company Name] places great emphasis on clear communication, attention to detail, and meeting project deadlines.With a growing portfolio of successful projects and satisfied clients, [Company Name] continues to establish itself as a leader in the prototyping industry. By investing in research and development, staying up-to-date with emerging technologies, and fostering a culture of innovation, the company is well-positioned to shape the future of prototyping.In conclusion, [Company Name] is a prototyping company based in the United States that is leading the way in revolutionizing the manufacturing industry. With its state-of-the-art facilities, diverse range of capabilities, and commitment to customer satisfaction, [Company Name] is adept at turning clients' ideas into tangible products through high-quality prototypes. With their dedication to innovation and exceptional service, [Company Name] is poised to remain at the forefront of the prototyping industry for years to come.