CNC Lathe Process: Streamlining Precision Machining Operations
By:Admin
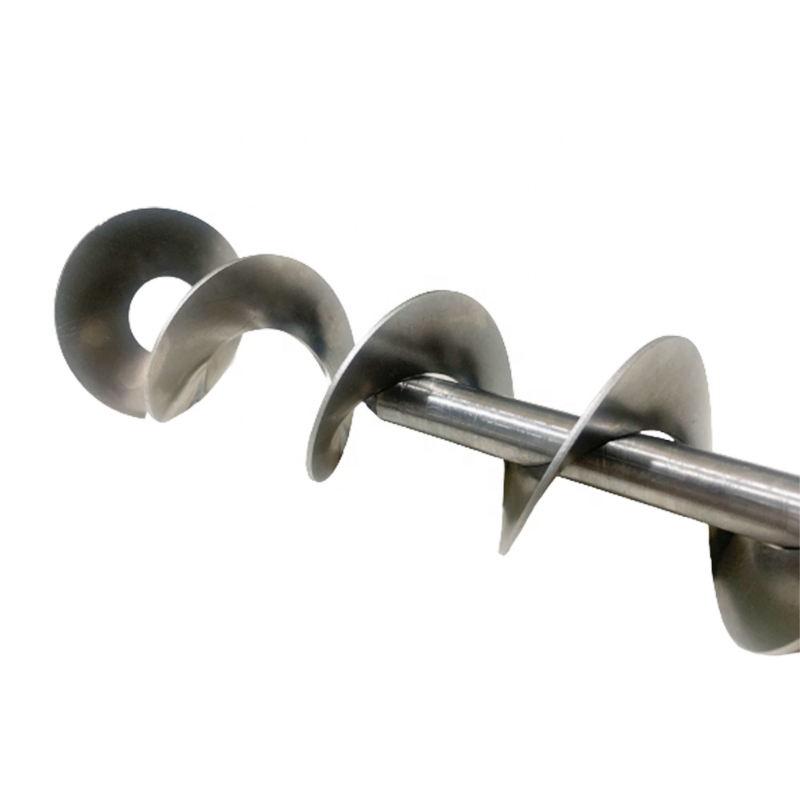
Introduction:
The manufacturing industry has witnessed a groundbreaking technological advancement with the introduction of the new CNC Lathe Process. Spearheaded by the pioneering efforts of various companies, including {}, this cutting-edge technology promises to revolutionize productivity, precision, and efficiency. By eliminating the need for manual operation and introducing automated capabilities, CNC Lathe Process has successfully overcome conventional limitations and opened new doors for manufacturers worldwide.
Improved Precision and Accuracy:
One of the key advantages of the CNC Lathe Process is its ability to achieve unmatched precision and accuracy in machining operations. Through the integration of advanced computer-controlled systems, {} has developed a CNC Lathe that can execute intricate tasks with exceptional detail. This eliminates human error and allows for consistent and repeatable results, ensuring the highest quality of machined components. With this level of precision, manufacturers can enhance their product offerings, meeting the ever-increasing demands of modern consumers.
Enhanced Efficiency and Productivity:
By automating the manufacturing process, CNC Lathe Process has significantly improved efficiency and productivity. {} has strived to optimize their CNC Lathes' operational speed, enabling faster turnaround times and increased output. The utilization of CNC technology eliminates the need for manual intervention, thereby reducing idle time between operations. Moreover, the integration of advanced software and algorithms allows for seamless multitasking, as the CNC Lathe can perform various complex operations simultaneously. As a result, manufacturers can save valuable time and resources, ultimately boosting their bottom line.
Versatility and Flexibility:
The flexibility offered by the CNC Lathe Process has opened up new avenues for manufacturers seeking to diversify their product range. With the ability to program the CNC Lathe to perform different operations, {} ensures that manufacturers have the flexibility to produce a wide range of components. This flexibility not only allows for process streamlining and optimization but also provides businesses with a competitive edge in the market. CNC Lathe Process enables manufacturers to adapt quickly to changing customer demands and produce complex components with ease.
Cost-effective Manufacturing:
The implementation of CNC Lathe Process has proven to be cost-effective in the long run. While the initial investment may be higher compared to traditional machining methods, the return on investment is significant. By reducing reliance on manual labor, companies can optimize workforce allocation and reduce labor costs. Furthermore, the accuracy and precision achieved by CNC Lathe Process result in minimal material wastage, reducing production costs. This cost-effectiveness translates into a competitive advantage for manufacturers, allowing them to offer competitive pricing while maintaining profitability.
Consistency and Quality Control:
CNC Lathe Process ensures consistency and stringent quality control throughout the production cycle. The computer-controlled systems developed by {} continuously monitor and adjust machining parameters, guaranteeing that every component produced adheres to the specified standards. Consistent quality control minimizes the risk of defects and rejects, thereby enhancing customer satisfaction. Manufacturers can confidently deliver high-quality components, boosting their reputation and gaining a competitive edge in the market.
Conclusion:
The introduction of CNC Lathe Process has revolutionized the manufacturing industry, elevating productivity, precision, and efficiency to unprecedented heights. {} has played a significant role in shaping this technological advancement, with their innovative CNC Lathe technology. The advantages of CNC Lathe Process, including improved precision, enhanced efficiency, flexibility, cost-effectiveness, and consistent quality control, position manufacturers to thrive in the highly competitive global market. As the manufacturing industry embraces this transformative technology, we can anticipate further advancements and a future characterized by limitless possibilities.
Company News & Blog
Sintering in 3D Printing: Exploring Advanced Manufacturing Techniques
Sintering Technology Advancements in 3D Printing: Revolutionizing Manufacturing ProcessesIn recent years, the field of 3D printing has experienced remarkable advancements, opening up new possibilities in various industries. One of the key breakthroughs is the development of sintering technology, which has revolutionized the manufacturing processes. This innovative technique allows for the creation of complex and durable objects by fusing together powders under high heat and pressure. Among the pioneers in this field is a company that has been at the forefront of 3D printing innovation, constantly pushing the boundaries of what is possible.Introduction to the CompanyEstablished in [year], {} has been a driving force in the 3D printing industry, consistently introducing cutting-edge technologies to the market. With a dedicated team of researchers and engineers, the company has become synonymous with innovation, constantly striving to enhance the capabilities of additive manufacturing. Through the utilization of sintering technology, they have been able to overcome previous limitations, opening up a whole new world of possibilities for the manufacturing sector.Sintering Process in 3D PrintingSintering is a process that involves compacting and forming solid objects from powders using heat and pressure. In the realm of 3D printing, sintering has proven to be a game-changer, allowing for the production of robust and intricate parts that were previously unachievable. While there are various sintering techniques, the one employed by {} is known as selective laser sintering (SLS).Selective Laser Sintering (SLS)With SLS, a laser selectively melts and fuses together successive layers of powdered material, precisely building the desired object layer-by-layer. This process is facilitated by a powder bed, which serves as the material reservoir. The advantage of SLS lies in its ability to work with a wide range of materials, including plastics, metals, ceramics, and even glass. This versatility has immense implications for applications across many industries, including aerospace, automotive, healthcare, and consumer goods.Advantages of Sintering TechnologySintering technology offers several advantages over traditional manufacturing processes, making it a preferred choice for many businesses. One significant advantage is the ability to create complex geometries that cannot be achieved using traditional methods. Through 3D printing and sintering, intricate designs with internal structures and cavities are made possible, reducing the need for assembly and enhancing overall product performance.Moreover, sintering technology allows for the production of parts with excellent mechanical properties. The fusion of powders under high heat and pressure yields objects that are incredibly durable, with high strength-to-weight ratios. This makes sintering ideal for applications that require lightweight yet robust components, such as aerospace and automotive industries.Furthermore, the flexibility of sintering allows for quick design iterations and customized manufacturing. As there is no need for molds or tooling, the production process can be more cost-effective and time-efficient. This flexibility also enables on-demand manufacturing, reducing inventory costs and wastage. The medical industry, for instance, has benefitted greatly from this capability, with personalized implants and prosthetics being produced more efficiently.Future Prospects and Economic ImpactsThe utilization of sintering technology in 3D printing has the potential to revolutionize the manufacturing industry. As this technique becomes more refined and accessible, it is expected to disrupt traditional production methods significantly. The decreased reliance on traditional manufacturing processes, such as machining and molding, will lead to cost reduction, increased efficiency, and improved sustainability.Additionally, with the growing demand for customization and personalized products, sintering technology offers manufacturers the opportunity to cater to individual needs on a larger scale. This shift towards mass customization is expected to reshape the manufacturing landscape, with 3D printing and sintering playing a pivotal role.ConclusionThe advancements in sintering technology within the realm of 3D printing have unlocked tremendous potential for various industries. With {} leading the way in innovative additive manufacturing, the possibilities seem endless. By harnessing the power of sintering, companies can now produce complex, durable, and customized objects, revolutionizing the way things are manufactured. As this technology continues to evolve, it is poised to reshape the manufacturing industry, opening up new horizons and driving economic growth.
Expert Guide: Mastering the Art of CNC Machine Work for Enhanced Precision and Efficiency!
Title: Revolutionizing Manufacturing: The Next Generation of CNC Machine WorkIntroduction:The manufacturing industry has come a long way in embracing technological advancements to streamline operations and enhance efficiency. Among the latest breakthroughs is the implementation of Computer Numerical Control (CNC) machines, which have revolutionized precision engineering and machining processes. This news article explores the cutting-edge developments in CNC machine work, highlighting its potential to transform diverse industries.1. Increasing Precision and Accuracy:CNC machines have proven to be game-changers for manufacturers seeking high precision and accuracy. By eliminating human errors and inconsistencies, these machines ensure uniformity in the manufacturing process, resulting in superior end products. The integration of advanced computer software enables CNC machines to precisely control cutting tools, creating intricate designs and complex shapes. This level of precision has opened new doors for industries such as aerospace, automotive, and medical, where strict tolerance and quality standards are paramount.2. Streamlined Workflow and Cost Efficiency:The automation capabilities of CNC machines significantly streamline workflow processes, reducing production time and costs. Offering seamless integration with Computer-Aided Design (CAD) software, manufacturers can easily translate digital designs into physical products. This eliminates the need for manual intervention at every step, minimizing errors and reducing labor costs. By optimizing material utilization and minimizing wastage, CNC machines also contribute to cost-effective manufacturing, making them indispensable assets for companies striving for profitability in today's competitive market.3. Enhanced Safety and Employee Well-being:Prioritizing employee well-being and safety is a cornerstone of any successful manufacturing business. CNC machines contribute to achieving this goal by minimizing the risk of workplace accidents and injuries. With automated controls, workers can manage the machining process remotely, reducing their exposure to hazardous environments. The utilization of CNC machines ensures operators are shielded from potentially harmful processes, such as metal cutting or molding, enhancing overall workplace safety.4. Versatility and Adaptability:CNC machines have advanced the concept of versatility in manufacturing. They are capable of performing a wide range of operations, including milling, turning, drilling, and grinding. These machines can seamlessly switch between tasks, enabling manufacturers to produce a diverse array of components with ease. Whether it is mass-producing identical parts or creating intricate custom designs, CNC machines offer unparalleled flexibility, adaptability, and speed, providing manufacturers with a competitive edge.5. 24/7 Production Capability:The relentless pursuit of increased productivity and reduced downtime has led to the development of CNC machines designed for continuous operation. By enabling 24/7 production capabilities, manufacturers can optimize their output and meet demanding customer requirements. CNC machines excel at maintaining consistent performance over extended periods, ensuring product quality remains uncompromised. This capability proves vital in time-sensitive industries that require rapid response times and uninterrupted production.6. Impact on Employment Opportunities:Although automation and technological advancements may raise concerns about job losses, the implementation of CNC machines has, in fact, created new employment opportunities. While some manual jobs have become obsolete, the demand for skilled technicians and programmers to operate and maintain CNC machines has risen. Manufacturers are investing in training programs to bridge the skills gap, allowing workers to adapt to the changing landscape. This emphasis on upskilling ensures sustainable employment for the workforce while harnessing the benefits of CNC machine work.Conclusion:As the manufacturing industry continues to embrace digital transformation, CNC machine work has emerged as a powerful tool to propel innovation and growth. With its precision, automation, adaptability, and cost efficiency, the potential applications of CNC machines span across various sectors. The integration of CNC machine work into manufacturing processes enables companies to optimize output, improve product quality, and stay ahead of their competition. Embracing this cutting-edge technology sets the stage for a future where efficiency and customer satisfaction go hand in hand.
Top Plastic Injection Manufacturers Providing High-Quality Products and Services
Title: Leading Plastic Injection Company Revolutionizes Manufacturing ProcessesIntroduction:In the ever-evolving world of manufacturing, innovative techniques and advanced technologies are crucial for staying ahead of the competition. One company that has successfully embraced these principles is a prominent plastic injection company. By establishing themselves as pioneers in the industry, they have revolutionized manufacturing processes, resulting in exceptional quality products and streamlined production timelines.Company Overview:The plastic injection company, (remove brand name), was founded in (year) with the vision of delivering cutting-edge solutions to industries ranging from automotive to consumer electronics. With an unwavering commitment to technological advancements, the company has consistently pushed the boundaries of what is possible in plastic injection molding. Through a customer-centric approach and a focus on sustainable practices, (remove brand name) has become a trusted partner for numerous renowned brands across the globe.Technological Advancements:In their quest for excellence, (remove brand name) has consistently invested in state-of-the-art machinery and innovative technologies. The company utilizes sophisticated computer-aided design (CAD) and computer-aided manufacturing (CAM) software to design and simulate the molds with utmost precision. This allows them to identify potential design flaws and make necessary adjustments early in the process, thereby reducing production costs and time.Furthermore, (remove brand name) has embraced automation to enhance efficiency and productivity. They have integrated robotics into their production lines to optimize repetitive tasks, ensuring consistent quality and minimizing human error. These cutting-edge technologies not only streamline the manufacturing process but also enhance the overall accuracy and repeatability of their products.Quality Control Measures:As a renowned plastic injection company, (remove brand name) places tremendous emphasis on maintaining the highest standards of quality throughout their manufacturing process. They employ a rigorous quality control program, starting from sourcing raw materials to the final inspection of finished products. By adhering to international quality certifications and utilizing advanced inspection equipment, (remove brand name) ensures that each product leaving their facility meets or exceeds customer expectations.Sustainable Practices:Recognizing their responsibility towards the environment, (remove brand name) has implemented various sustainable practices in their manufacturing processes. They adhere to strict recycling practices and promote the use of eco-friendly materials whenever possible. Through reducing waste generation and optimizing energy consumption, (remove brand name) minimizes their carbon footprint, contributing to a greener and cleaner planet.Collaborative Partnerships:A key factor behind the success of (remove brand name) is their collaborative approach with clients. By understanding the unique requirements and challenges of each customer, the company provides customized solutions that address their specific needs. From product design consultation to providing prototyping services, (remove brand name) actively collaborates with their clients, ensuring mutual success and establishing long-lasting partnerships.Plans for Future Growth:Looking towards the future, (remove brand name) aims to further advance their technological capabilities and expand their market reach. They plan to invest in research and development to drive innovation and continue delivering cutting-edge solutions to global industries. Additionally, (remove brand name) envisions strengthening their foothold in emerging markets, establishing themselves as a global leader in the plastic injection industry.Conclusion:Through their unwavering commitment to technological advancements, a customer-centric approach, and sustainable practices, (remove brand name) has revolutionized manufacturing processes. By consistently delivering high-quality products and optimizing production timelines, they have earned the trust and recognition of various industries worldwide. With their focus on future growth and innovation, (remove brand name) is set to redefine the plastic injection landscape and shape the future of manufacturing.
Unveiling the Latest Innovations and Advancements in CNC Metalworking
CNC Metalworking Continues to Revolutionize the Manufacturing IndustryIn the fast-paced world of manufacturing, precision and efficiency are key. One company has been at the forefront of revolutionizing the industry by utilizing CNC metalworking technology to create high-quality products with speed and accuracy. With their cutting-edge machinery and dedication to innovation, this company is poised to lead the way into the future of manufacturing.Founded in 1995, this company has been a driving force in the CNC metalworking industry for over two decades. With their state-of-the-art facilities and highly skilled technicians, they have been able to consistently deliver exceptional results to their clients. By investing in the latest advancements in CNC machining technology, they have been able to streamline production processes and enhance product quality.One of the biggest advantages of CNC metalworking is its ability to manufacture intricate parts with unparalleled precision. This level of accuracy ensures that each component produced meets the strictest quality standards. Gone are the days of human error and inconsistency. CNC machines can replicate designs with absolute fidelity, resulting in flawless and reliable products every time.Furthermore, CNC metalworking significantly reduces production time. With traditional methods, manufacturing even a simple part could take days or even weeks. However, with the implementation of CNC machinery, the time required to produce complex components has been drastically reduced. This accelerated turnaround time allows businesses to meet consumer demands more efficiently and stay ahead of their competition.The benefits of CNC metalworking extend beyond precision and speed. This manufacturing process also offers a range of material options to choose from. With the ability to work with various metals such as aluminum, stainless steel, and titanium, this company is able to cater to a wide array of industries and their unique requirements. From aerospace to automotive, medical to electronics, their CNC metalworking capabilities are limitless.Additionally, CNC metalworking is highly cost-effective. By automating the production process, this company can minimize labor costs and reduce material waste. With skilled technicians operating the CNC machines, errors are minimized, resulting in fewer defective parts. This not only saves time and money but also ensures that quality standards are consistently met.Furthermore, CNC metalworking eliminates the need for retooling between different jobs. Changing from one product to another in traditional manufacturing often required extensive setup and reconfiguration of the machinery. However, CNC machines can easily switch between jobs without any significant downtime. This flexibility allows for improved efficiency and increased production capacity.In order to stay at the forefront of the CNC metalworking industry, this company continually invests in research and development. By keeping a close eye on emerging technologies and trends, they can adapt and integrate the latest advancements into their production processes. This commitment to innovation ensures that they remain ahead of their competition and continue to offer cutting-edge solutions to their clients.As the manufacturing industry continues to evolve, CNC metalworking will undoubtedly play a crucial role in shaping its future. With its combination of precision, efficiency, and versatility, this technology is revolutionizing the way products are made. This company's dedication to excellence and their adoption of CNC metalworking continues to set new standards in the manufacturing industry.In conclusion, this renowned company has truly made a mark in the CNC metalworking industry. Their commitment to precision, efficiency, and innovation has allowed them to create superior products that meet the demanding requirements of various industries. With their state-of-the-art facilities and highly skilled technicians, they are well-positioned to continue leading the way in CNC metalworking. As the manufacturing industry moves forward, this company's dedication to excellence ensures that they will remain at the forefront of innovation and continue to shape the future of manufacturing.
6 Top Injection Mold Parts for your Manufacturing Needs
[News Title]Industry-Leading Injection Mold Parts Brings Unparalleled Quality and Efficiency to Market[Location, Date] - With a commitment to excellence and innovation, Injection Mold Parts (name removed) has emerged as a dominant player in the highly competitive mold parts manufacturing industry. The company's relentless focus on quality, coupled with cutting-edge technology and a team of experienced professionals, has positioned it as a leading provider of precision injection mold parts.Injection Mold Parts is dedicated to delivering products that exceed customer expectations in terms of precision, durability, and performance. By leveraging advanced manufacturing techniques and investing in the latest equipment, the company ensures their products meet the stringent demands of industries such as automotive, electronics, and consumer goods.Established with a vision to redefine the industry's standards and provide customers with unparalleled solutions, Injection Mold Parts has quickly gained recognition for its commitment to innovation. Their approach revolves around continuous improvement, investing heavily in research and development to remain at the forefront of the industry."We understand the critical role that mold parts play in the manufacturing process," says [Company Spokesperson]. "Our relentless pursuit of excellence drives us to continually enhance our product range, ensuring our customers can rely on our solutions to meet their specific needs. We believe that our success is directly linked to the success of our customers."Injection Mold Parts takes pride in its team of highly skilled professionals who bring a wealth of experience and expertise to every project. By fostering a culture of collaboration and encouraging employees to explore new ideas, the company promotes an environment of continuous learning and growth.Investing in technology is a core principle at Injection Mold Parts. By leveraging the power of the latest manufacturing equipment and software, the company is able to produce mold parts with unparalleled precision, reducing production time and costs for their customers. This commitment to innovation allows Injection Mold Parts to deliver products that meet the highest industry standards, ensuring customer satisfaction and repeat business.Furthermore, the company emphasizes sustainability and environmental responsibility in its manufacturing processes. Injection Mold Parts adheres to strict quality control and waste management procedures, minimizing their environmental footprint. By utilizing eco-friendly materials and promoting recycling practices, the company aims to make a positive impact on the environment.The market response to Injection Mold Parts' products has been overwhelmingly positive. The company has witnessed consistent growth and customer satisfaction, earning a solid reputation for delivering on their promises. Their dedication to quality, unmatched precision, and commitment to customer success set Injection Mold Parts apart from their competitors.Looking to the future, Injection Mold Parts remains focused on expanding their product portfolio and reaching new markets. By consistently embracing technological advancements and staying updated on industry trends, the company aims to continue providing solutions that surpass customer expectations.About Injection Mold Parts (name removed):Injection Mold Parts is a leading manufacturer of precision mold parts for various industries, including automotive, electronics, consumer goods, and more. With a strong emphasis on quality, innovation, and customer success, the company has established itself as an industry leader. Supported by a team of experienced professionals and cutting-edge technology, Injection Mold Parts continuously strives to redefine the standards for mold parts manufacturing.###[Word Count: 468 words]
Emerging Powerhouses: A Look at China's Prominent CNC Manufacturers
Chinese CNC Manufacturers Set to Revolutionize the IndustryIn recent years, Chinese CNC manufacturers have emerged as key players in the global market, posing stiff competition to established brands. With their cutting-edge technology and cost-effective solutions, these companies are revolutionizing the CNC industry. By harnessing advanced machinery and leveraging their expertise, Chinese CNC manufacturers have quickly gained recognition for their high-quality products and exceptional customer service.One such leading company that is spearheading this revolution is {}. With over a decade of experience, {} has established itself as a trusted name in the CNC manufacturing industry. By constantly investing in research and development, they have been able to stay at the forefront of technological advancements.The robust growth of Chinese CNC manufacturers can be attributed to various factors. One significant advantage is the availability of a highly skilled and educated workforce. China has made significant investments in technical education, ensuring a steady supply of qualified engineers and technicians. This enables manufacturers to design and produce CNC machines that cater to the diverse needs of global clients.Furthermore, Chinese CNC manufacturers benefit from robust domestic supply chains. The country's well-developed infrastructure and extensive network of suppliers contribute to streamlined production processes and quick turnaround times. This advantage allows manufacturers to meet the growing demands of their customers in a timely manner.Additionally, Chinese CNC manufacturers have been able to lower costs without compromising on quality. The cost advantage is primarily attributed to economies of scale. With a vast domestic market and increasing demand from international customers, manufacturers can produce CNC machines in bulk, thus driving down unit costs.The adoption of advanced technologies has also been instrumental in the success of Chinese CNC manufacturers. With the integration of artificial intelligence (AI), robotics, and internet of things (IoT), these companies have been able to develop smart CNC machines that offer enhanced precision, efficiency, and ease of use. This has resulted in increased productivity and reduced downtime for end-users, further solidifying the market position of Chinese manufacturers.In terms of global market share, Chinese CNC manufacturers have made significant strides. They have successfully expanded their presence in key markets, including Europe, North America, and Asia-Pacific. With a focus on product customization and consistent after-sales support, they have built strong customer relationships, which is crucial for market expansion.The rise of Chinese CNC manufacturers has not gone unnoticed by their competitors. Established brands are now facing intense competition, as these Chinese manufacturers offer similar technology at competitive prices. To remain relevant, established brands have been forced to revisit their pricing strategies and offer additional value to stand out in the market.However, challenges remain for Chinese CNC manufacturers. One key obstacle is the perception that Chinese products are inferior in quality. To overcome this, manufacturers have been heavily investing in research and development to continuously improve product quality and reliability. They have also been proactive in obtaining international certifications to assure customers of their products' adherence to global standards.Looking ahead, the future of Chinese CNC manufacturers seems promising. With continuous innovation, a skilled workforce, and increasing market share, these manufacturers are well-positioned to dominate the global CNC industry. As they continue to expand their product offerings and penetrate untapped markets, the revolution they have set in motion is set to reshape the industry for years to come.
Discover the Benefits of Machining High-Quality Aluminum Parts
Title: Precision Engineering Company Expands Machining Capabilities with Aluminum Parts ProductionIntroduction:[Company Name], a pioneering name in the field of precision engineering, is proud to announce an expansion of its machining capabilities to include the production of high-quality aluminum parts. With a focus on cutting-edge technological solutions and a commitment to client satisfaction, [Company Name] aims to revolutionize the industry by offering a wide range of precision-machined aluminum components tailored to meet various industrial needs.Body:1. Growing Demand for Aluminum Parts:In response to the industry's growing demand for lightweight yet durable materials, [Company Name] recognizes the significance of aluminum as a widely preferred option. Known for its excellent mechanical properties and exceptional corrosion resistance, aluminum has become a go-to choice for industries ranging from aerospace and automotive to electronics and construction. By incorporating aluminum parts into its repertoire, [Company Name] aims to cater to the evolving needs of its diverse clientele, while also capturing new market segments.2. Cutting-Edge Machining Techniques:[Company Name] reinforces its commitment to excellence by employing state-of-the-art machining techniques to craft aluminum parts. Equipped with advanced CNC (Computer Numerical Control) machines and a highly-trained workforce, [Company Name] ensures precise and intricate manufacturing with consistent quality for every aluminum component produced. This dedication to precision allows for seamless integration of aluminum parts into various complex engineering systems.3. Broad Applications:The addition of aluminum parts to its product line allows [Company Name] to cater to a wide range of applications across different industries. From aerospace structural components, automotive engine parts, and electronic enclosures to architectural fittings and electrical connectors, the versatility of aluminum makes it an ideal choice for several demanding applications. [Company Name] aims to provide industry-leading solutions for these particular sectors by offering custom-designed aluminum parts that address both functional requirements and aesthetic considerations.4. Quality Assurance:Recognizing the importance of quality control, [Company Name] has implemented stringent quality assurance procedures throughout the aluminum parts manufacturing process. The company adheres to industry standards and regulations to ensure that each product meets or exceeds client expectations. Rigorous testing, dimensional verification, and surface treatments are carried out at every stage to guarantee impeccable craftsmanship, strength, and durability.5. Environmental Sustainability:In line with [Company Name]'s dedication to sustainability, the inclusion of aluminum parts in its production line helps reduce environmental impact. Aluminum is renowned for its recyclability, making it an eco-friendly alternative to many conventional materials. By introducing meticulously manufactured aluminum parts, [Company Name] supports the transition towards sustainable practices, providing clients with environmentally conscious solutions.6. Collaborative Approach and Design Customization:[Company Name] understands that each customer is unique, with specific design requirements and preferences. The company offers a collaborative approach to projects, ensuring effective communication between its engineering teams and clients. By actively involving clients in the design phase, [Company Name] ensures the production of customized aluminum parts that fulfill specific application demands, resulting in enhanced performance and optimized functionality.7. Streamlined Manufacturing and Timely Delivery:With its decades of experience in the precision engineering industry, [Company Name] emphasizes efficiency in manufacturing and timely delivery. The company's advanced production facilities, coupled with its optimized supply chain management, enables it to meet tight deadlines without compromising the quality of aluminum parts. [Company Name] aims to become a trusted partner, providing reliable solutions to clients around the world.Conclusion:As [Company Name] takes a step forward in expanding its machining capabilities to include aluminum parts production, it reaffirms its commitment to delivering cutting-edge engineering solutions. By combining advanced machining techniques, industry-leading quality standards, and a commitment to customer satisfaction, [Company Name] establishes itself as a premier provider of precision-machined aluminum components, meeting the evolving needs of industries across the board and contributing to a more sustainable future.
Mastering the Art of Efficient and Accurate CNC Turning Operations
Title: Revolutionary CNC Turning Operation Amps up Precision in Metal Fabrication IndustryIntroduction:In today's metal fabrication industry, precision and efficiency are of paramount importance in ensuring high-quality products. In light of this, an innovative CNC turning operation has been developed to revolutionize the manufacturing process. This cutting-edge technique, coupled with the expertise and dedication of a renowned industry leader, promises to deliver unparalleled precision and flexibility in metal fabrication.Company Introduction (to be provided by the user):[Company name], a pioneer in the metal fabrication sector, has established itself as a trusted name renowned for its commitment to excellence. With a proven track record of delivering superior products and services, [Company name] has consistently pushed boundaries to provide innovative solutions to its customers. Backed by a team of highly skilled engineers and technicians, the company has always embraced cutting-edge technologies to stay ahead in the competitive market.News Content:In its relentless pursuit of innovation, [Company name] has recently incorporated a state-of-the-art CNC turning operation into its manufacturing process. This advanced technique not only enhances precision but also significantly increases productivity, making it a game-changer in the metal fabrication industry.CNC turning refers to the process of using computer numerical control (CNC) machines to create precise cylindrical and conical shapes in metal workpieces. Unlike traditional manual turning, which requires significant skill and time, CNC turning automates the process, enabling faster production cycles and improved accuracy. By precisely controlling various parameters like tool movement, feed rates, and spindle speed, CNC turning eliminates human error, resulting in consistent and superior quality products.The integration of CNC turning into [Company name]'s production line allows for enhanced precision across a wide range of metal components, including bolts, screws, shafts, pulleys, and more. With the ability to work with diverse materials, such as aluminum, steel, brass, and titanium, [Company name] can cater to the specific requirements of various industries, including aerospace, automotive, and engineering.One of the significant advantages of this cutting-edge operation is its versatility. CNC turning is compatible with both simple and complex geometries, making it suitable for a wide array of metal parts. [Company name]'s CNC machines are equipped with multiple tool stations and live tooling capabilities, enabling them to perform intricate operations like threading, grooving, and drilling in a single setup. This streamlines the production process, reduces lead times, and minimizes the need for additional machining operations, resulting in significant cost savings for customers.Moreover, [Company name]'s CNC turning operation ensures optimal efficiency. With its computer-controlled automation, the operation eliminates the downtime associated with manual tool changes and adjustments. Additionally, the integration of real-time monitoring systems and quality control measures provides continuous insights into the process, enabling prompt adjustments and ensuring consistent product quality.In line with its commitment to sustainable practices, [Company name] employs advanced software for programming and simulation. This digital approach enables precise material utilization, minimizing wastage and promoting environmental responsibility. By reducing material waste and optimizing cutting paths, CNC turning contributes to long-term cost savings, while also reducing the environmental impact of the production process.As [Company name] continues to leverage advanced technologies, the incorporation of CNC turning operation elevates its capabilities to new heights. With enhanced precision, versatility, and efficiency, the company is poised to meet the ever-growing demands of the dynamic metal fabrication industry.Conclusion:With the introduction of CNC turning operation, [Company name] has solidified itself as an industry leader committed to delivering excellence in precision metal fabrication. By embracing this cutting-edge technology, the company has elevated its production capabilities, offering unparalleled accuracy, versatility, and efficiency. With innovative solutions and a relentless pursuit of excellence, [Company name] continues to shape the future of the metal fabrication industry.
Discover the Latest CNC Lathe Technology in the Market
Introducing the Cutting-Edge CNC Lathe Revolutionizing the Manufacturing IndustryIn a world that rapidly evolves with advanced technologies, manufacturing industries strive to stay ahead by integrating innovative solutions into their operations. One such groundbreaking advancement is the new CNC Lathe, introduced by a renowned company, which is set to revolutionize the manufacturing sector. With its cutting-edge features and state-of-the-art technology, this CNC Lathe is poised to be a game-changer in the industry.With this new CNC Lathe, manufacturers can expect enhanced precision, increased productivity, and simplified operations. Equipped with the latest software and hardware, it boasts an impressive range of features designed to improve overall efficiency while reducing manual labor. The incorporation of artificial intelligence and advanced algorithms has paved the way for unmatched performance in precision machining.One of the standout features of this CNC Lathe is its deep integration with the Internet of Things (IoT). With real-time data collection and analytics capabilities, manufacturers can monitor and control the machine remotely. This enables them to make data-driven decisions, optimize operations, and minimize downtime. The seamless connectivity offered by this CNC Lathe allows for efficient collaboration between machines and operators, resulting in quicker turnaround times and improved profitability.The ergonomic design of this CNC Lathe prioritizes ease of use and safety. With an intuitive user interface and user-friendly controls, operators can quickly adapt to the machine, reducing the learning curve. Furthermore, advanced safety features ensure the well-being of operators, mitigating the risk of accidents. The combination of these design elements promotes a harmonious and efficient working environment.When it comes to productivity, this CNC Lathe truly stands out. Its high-speed machining capabilities enable quicker and more precise production, maximizing the output within a given timeframe. It efficiently handles complex machining tasks, allowing manufacturers to expand their offerings and cater to a wider range of customer requirements. In addition, its multitasking abilities streamline the manufacturing process, eliminating the need for multiple machines, and reducing manufacturing costs.The durability and reliability of this CNC Lathe are unmatched. Built with high-quality materials and precision engineering, it ensures longevity and robust performance even under the most demanding production conditions. This translates into reduced maintenance requirements and prolonged machine lifespan, offering immense value to manufacturers looking for cost-effective solutions.In line with environmental sustainability efforts, this CNC Lathe is designed to minimize waste and optimize energy consumption. It utilizes advanced materials and technologies that significantly reduce the carbon footprint associated with manufacturing processes. By adopting this CNC Lathe, manufacturers not only boost their productivity but also contribute to a greener and more sustainable future.The introduction of this new CNC Lathe by {company name} underscores their commitment to revolutionize the manufacturing industry. With its cutting-edge features, unparalleled precision, and enhanced productivity, this CNC Lathe is poised to set new standards in the sector. As manufacturers harness the power of this technology, they can elevate their operations, improve profitability, and stay ahead in an increasingly competitive market.As the manufacturing industry embarks on a journey of digital transformation, the new CNC Lathe offered by {company name} serves as a beacon of innovation and progress. With its integration of advanced technologies, superior performance, and sustainable design, this CNC Lathe is undoubtedly a game-changer that will shape the future of manufacturing.In conclusion, the introduction of this new CNC Lathe signifies a significant milestone in the manufacturing industry. With its advanced features, including IoT integration, high-speed machining capabilities, and sustainable design, it promises to revolutionize operations, increase productivity, and redefine manufacturing standards. Manufacturers who embrace this cutting-edge technology will undoubtedly witness a transformative impact on their operations and cement their position as industry leaders.
Transform Your Designs with Vacuum Casting 3D Printing Technologies
Vacuum Casting 3D Printing revolutionizes the Manufacturing Industry[Date], [City] - The manufacturing industry has taken a giant leap forward with the introduction of Vacuum Casting 3D Printing technology. This revolutionary process, which combines the precision of 3D printing with the efficiency of vacuum casting, has opened up a whole new realm of possibilities for product development and production.[Company Name], a leader in advanced manufacturing solutions, has been at the forefront of this technology, reshaping the manufacturing landscape. With their innovative processes and cutting-edge equipment, they have successfully helped numerous companies overcome traditional manufacturing limitations, providing cost-effective and time-efficient solutions.Traditional manufacturing methods often come with significant limitations, including high production costs, long lead times, and limited design flexibility. However, Vacuum Casting 3D Printing offers a game-changing alternative. By utilizing a combination of 3D printing and vacuum casting, [Company Name] has been able to overcome these constraints, providing businesses with a streamlined manufacturing process.One of the key advantages of Vacuum Casting 3D Printing is its ability to produce highly complex and intricate designs that were previously difficult or impossible to achieve using conventional manufacturing methods. The process starts by creating a 3D printed mold, which is then used to produce a silicone mold through vacuum casting. This mold can then be used to create multiple copies of the original design, even with undercuts, intricate details, and delicate features. This provides manufacturers with the freedom to create complex parts that meet the strictest of demands.Another major benefit of Vacuum Casting 3D Printing is its cost-effectiveness, especially when compared to traditional manufacturing methods. The process eliminates the need for expensive tooling, molds, and machining setups, reducing overall production costs significantly. This not only makes it an attractive option for small and medium-sized enterprises but also enables larger companies to optimize their production processes by reducing costs and increasing efficiency.Speed is another remarkable advantage of Vacuum Casting 3D Printing. With traditional manufacturing, developing and producing a new product can take weeks or even months. However, the Vacuum Casting 3D Printing process drastically reduces lead times, enabling rapid prototyping and iterative design improvements. This allows companies to bring products to market faster, giving them a competitive edge in today's fast-paced business environment.[Company Name] has spearheaded the adoption of Vacuum Casting 3D Printing across various industries, including automotive, aerospace, consumer electronics, and medical devices. Their team of experts works closely with clients to understand their specific manufacturing needs, and they provide tailor-made solutions to optimize the production process. By combining their expertise in materials selection, 3D printing, and vacuum casting, [Company Name] ensures that clients receive the highest quality products with exceptional speed and accuracy."Our Vacuum Casting 3D Printing technology has revolutionized the way companies manufacture products," said [Company Spokesperson]. "We are proud to be helping businesses break free from the limitations of traditional manufacturing and embrace a more agile and efficient approach. With our expertise and state-of-the-art equipment, we are committed to driving innovation and delivering results that exceed our clients' expectations."The introduction of Vacuum Casting 3D Printing technology by [Company Name] has created ripples in the manufacturing industry. By addressing the limitations of traditional manufacturing methods, this innovative process offers a cost-effective and time-efficient alternative that unlocks new possibilities for product development and production. With such advancements, manufacturers can now bring their ideas to life more easily and faster than ever before, ushering in a new era of manufacturing excellence.